-
Plastic Profile Extruder Machine
-
WPC Profile Extruder Machine
-
PVC Profile Extruder
-
PVC Panel Production Line
-
PVC Pipe Production Line
-
PVC Sheet Production Line
-
PE Sheet Extruder
-
PP Hollow Board Extrusion Line
-
Plastic Pipe Production Line
-
Plastic Sheet Extrusion Line
-
Plastic Board Extrusion Line
-
Plastic Pelletizing Machine
-
Plastic Auxiliary Equipment
Automatic Ceiling Wall Plastic PVC Panel Production Line Home Interior Decoration Making Machine
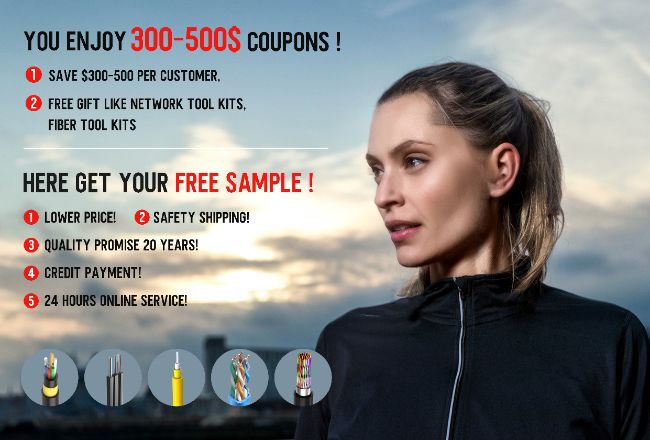
Contact me for free samples and coupons.
Whatsapp:0086 18588475571
Wechat: 0086 18588475571
Skype: sales10@aixton.com
If you have any concern, we provide 24-hour online help.
xName | PVC Panel Production Line | Material | PVC |
---|---|---|---|
Color | Green,Other Colors Can Be Customized | Control System | PLC |
Material Width | 200-600mm,Other Width Can Be Customized | Power Supply | 380V/50HZ,Other Power Can Be Customized |
Production Capacity | 100-380kg/h | Motor Power | 22-75KW |
Payment | T/T | Warranty | 12 Months |
Highlight | Ceiling PVC Panel Production Line,380kg/h PVC Panel Production Line,Automatic PVC Panel Making Machine |
PVC Panel Production Line
1. Production Introduction
PVC wall panels, also known as PVC decorative panels, are wall materials used for interior decoration. They are waterproof, fireproof, easy to clean, and environmentally friendly, so they are widely used in the construction and decoration industries.
2. Production Feature
(1) Efficient production: The PVC wall panel production line adopts automated equipment and processes to achieve high-efficiency production. Through continuous extrusion and automated operations, production efficiency can be greatly improved and labor costs and time waste reduced.
(2) Flexibility: PVC wall panel production lines can be adjusted and customized according to customer needs and market changes. The parameters of the extruder can be adjusted, and the design of the cutter and mold can be changed to meet the production requirements of PVC wall panels of different specifications, sizes and textures.
(3) Resource utilization: PVC wall panel production lines usually have waste recycling systems that can recycle and reuse waste materials generated during the production process. This helps reduce waste emissions, lower production costs, and is environmentally friendly.
(4) Quality control: The PVC wall panel production line is equipped with advanced testing equipment and quality control systems, which can monitor and adjust the production process in real time to ensure product quality and consistency. By testing indicators such as size, strength, appearance, etc., product defects can be eliminated and high-quality PVC wall panel products can be provided.
(5) Safety: PVC wall panel production lines usually have safety protection measures, such as emergency stop devices, protective covers, etc., to ensure the safety of operators. In addition, the PVC material used in the PVC wall panel production line itself has fireproof, waterproof and other properties, which increases the safety performance of the wall panels.
(6) Environmental protection: The PVC material used in the PVC wall panel production line is an environmentally friendly material that is renewable and recyclable. Compared with other wallboard materials, such as wood or gypsum board, PVC wallboard has less impact on the environment during production and use, and meets the requirements of sustainable development.
3. Product Configuration
Equipment Model | Production | Motor Power | Width |
KSJSZ-51/105 | 100-160kg/h | 22KW | 200-250mm |
KSJSZ-55/110 | 15-200kg/h | 30KW | 250-350mm |
KSJSZ-65/132 | 220-280kg/h | 37KW | 400-600mm |
KSJSZ-65/138 High Speed Machine |
240-300kg/h | 45KW | 400-600mm |
KSJSZ-80/156 | 300-380kg/h | 55-75KW | 600-800mm |
Note: In addition to the above configurations, our company can also customize according to customer needs.
4. Payment:
30% as advance payment by T/T after signed contract; 70% as balance before delivery by T/T .
5. The seller will provide the actual electric, pneumatic, hydraulic, mechanical parts circuit diagram for each unite of the machine with English language in addition to the original operation manual of the machine that contains the operation instruction, safety instruction, and troubleshooting with parts list for easy order necessary spare parts in the future.
6. Test run in the buyer’s factory: Seller send engineer for supervision of installation, training and test. The test will be finished in about 7-10 days if necessary preparations are made by the buyer such as water, electricity. Materials, work space, labors and so on. The round airplane tickets, visa cost, food, hotel fee and medical insurance of the engineer for installation and test run are paid by the buyer. The buyer pay USD150/per day as subsidy for the engineer.